Five common bucket conveyor feeding issues
This blog explores common feed issues that bucket conveyors may encounter.
Problem 1: Uneven feed distribution
Conveyor feeding issues are often design issues. When products are conveyed to the conveyor at right angles, the problem of uneven distribution of the products in the barrel often occurs. If the problem of uneven distribution is not addressed, uneven product flow can cause uneven wear on the bucket surface and can also cause the bucket to fill and overflow. Therefore, the conveyor equipment can be designed as a chamfered feeding chute, which can avoid this problem.
Problem 2: The bucket is often full
This problem is usually caused by incorrect device settings. Generally, the slower speed setting of the conveyor will reduce the bucket load, which will cause the bucket to be full. Increasing the conveyor speed to 2/3 or 67% of the bucket's maximum filling speed will avoid the problem that the bucket is often full.
Problem 3: Feed the bucket before the conveyor runs
Feed problems may occur if the bucket conveyor is not running at full speed before the bucket is loaded. The solution to this problem is to start the bucket elevator first, and then feed it after running for a while. Similarly, before stopping the bucket conveyor, the feed should be stopped to ensure that all material is emptied from the conveyor.
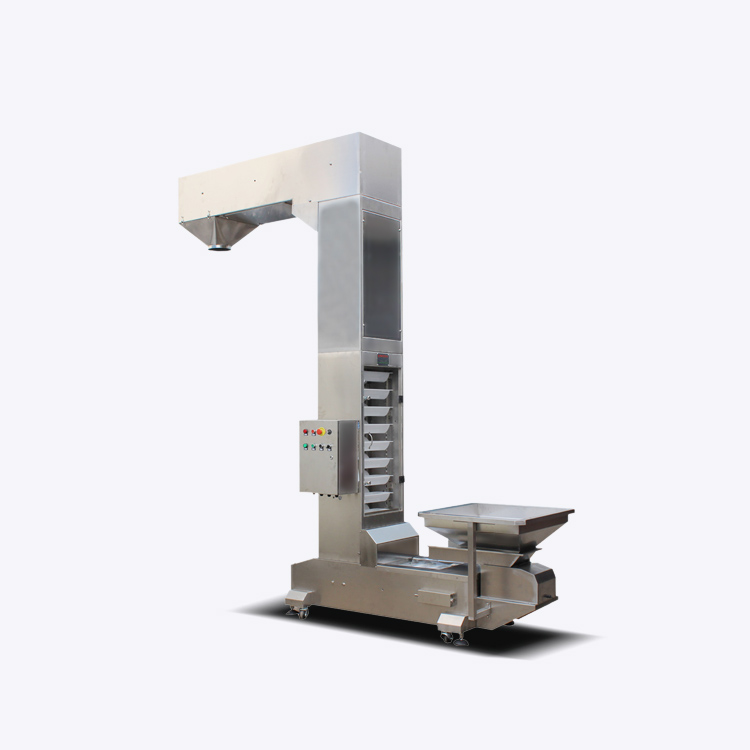
Problem 4: Product drop height is too high at the feed
Due to improper equipment design, this conveyor feeding problem occurred. To ensure optimal product transfer from the upstream process to the bucket conveyor, the drop height should be as small as possible. This provides gentler product delivery, maintaining product integrity while reducing the amount of dust. Higher discharge heights can also cause some products to pop up and can cause seal problems at the feed.
If the upstream process is difficult to lower or modify, the usual solution is to raise the lower part of the bucket conveyor. For example, all Volvod machines are equipped with adjustable floor supports, which makes it easy to change the height of the equipment. If needed, lower heights can be used to accommodate larger heights.
Problem 5: Lack of dust collection
This feeding problem is usually caused by the use of appropriate dust collection systems. Without a proper dust collection system, fine powder can be carried throughout the conveyor, causing deposits on equipment pulleys, ledges and other flat horizontal surfaces. Eventually, the accumulation of dust becomes severe enough to cause mispositioning of the conveyor belt. To eliminate feed problems with this conveyor, a conveyor equipped with a dust collection system is required.
If you can't solve the problem during the use of the machine, you can contact us, we will be happy to solve your problem for you.
Problem 1: Uneven feed distribution
Conveyor feeding issues are often design issues. When products are conveyed to the conveyor at right angles, the problem of uneven distribution of the products in the barrel often occurs. If the problem of uneven distribution is not addressed, uneven product flow can cause uneven wear on the bucket surface and can also cause the bucket to fill and overflow. Therefore, the conveyor equipment can be designed as a chamfered feeding chute, which can avoid this problem.
Problem 2: The bucket is often full
This problem is usually caused by incorrect device settings. Generally, the slower speed setting of the conveyor will reduce the bucket load, which will cause the bucket to be full. Increasing the conveyor speed to 2/3 or 67% of the bucket's maximum filling speed will avoid the problem that the bucket is often full.
Problem 3: Feed the bucket before the conveyor runs
Feed problems may occur if the bucket conveyor is not running at full speed before the bucket is loaded. The solution to this problem is to start the bucket elevator first, and then feed it after running for a while. Similarly, before stopping the bucket conveyor, the feed should be stopped to ensure that all material is emptied from the conveyor.
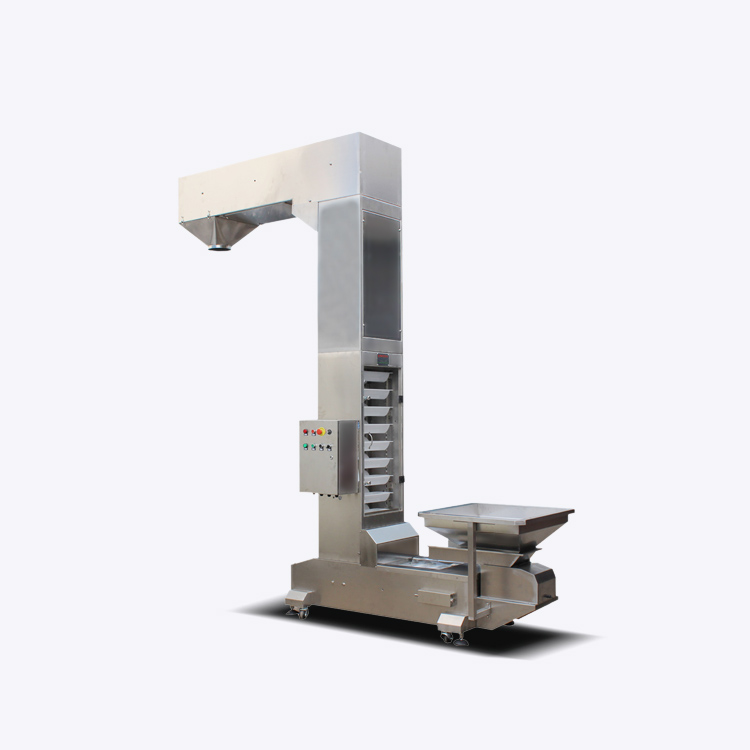
Problem 4: Product drop height is too high at the feed
Due to improper equipment design, this conveyor feeding problem occurred. To ensure optimal product transfer from the upstream process to the bucket conveyor, the drop height should be as small as possible. This provides gentler product delivery, maintaining product integrity while reducing the amount of dust. Higher discharge heights can also cause some products to pop up and can cause seal problems at the feed.
If the upstream process is difficult to lower or modify, the usual solution is to raise the lower part of the bucket conveyor. For example, all Volvod machines are equipped with adjustable floor supports, which makes it easy to change the height of the equipment. If needed, lower heights can be used to accommodate larger heights.
Problem 5: Lack of dust collection
This feeding problem is usually caused by the use of appropriate dust collection systems. Without a proper dust collection system, fine powder can be carried throughout the conveyor, causing deposits on equipment pulleys, ledges and other flat horizontal surfaces. Eventually, the accumulation of dust becomes severe enough to cause mispositioning of the conveyor belt. To eliminate feed problems with this conveyor, a conveyor equipped with a dust collection system is required.
If you can't solve the problem during the use of the machine, you can contact us, we will be happy to solve your problem for you.