Classification of Automatic Control Systems for Full Automatic Packing Machine
As an important equipment for automated production, the automatic control system of the full automatic packing machine can be classified from different angles.
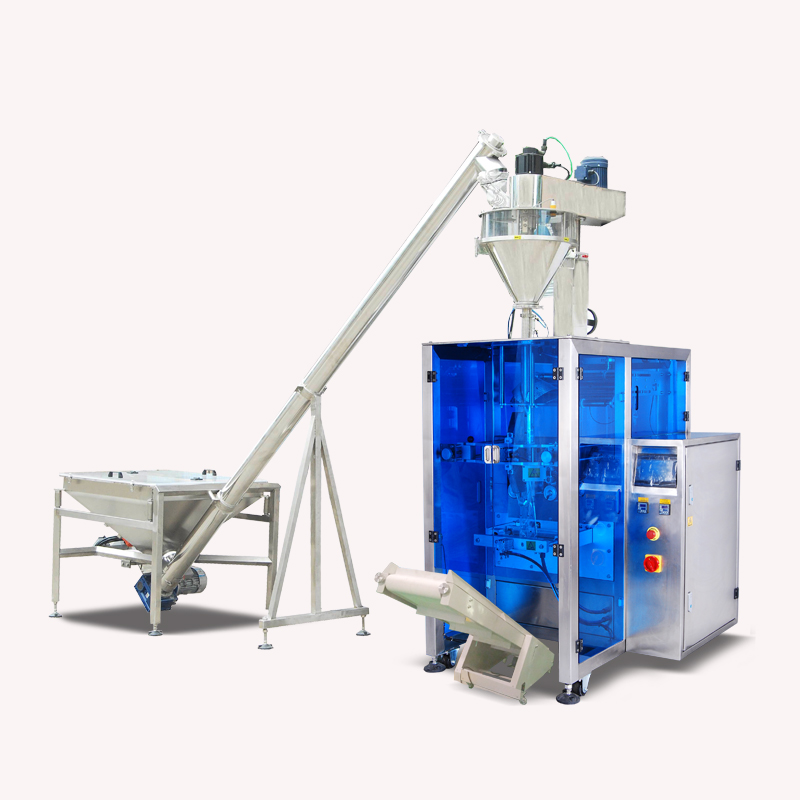
(—) Classification according to the change law of the input amount
1. Constant value control system
The so-called constant value is the abbreviation of constant given value. The given value of the system is unchanged, and the output of the system is required to be kept constant accordingly. During the packing process, some parameters are required to be kept at a normal standard value, which is the given value. Such as temperature control, material weight control, flow control, etc. are such systems.
2. Program control system
The given value of the system is a pre-determined time function that changes according to a predetermined law. The task of the system is to make the controlled quantity change according to a predetermined law with a predetermined accuracy.
3. Servo control system
Following control system is also called tracking control system. The characteristic of this type of system is that the given value is constantly changing, and the change law is unknown. The purpose of the control system is to make the controlled parameter follow the given value change quickly and accurately. The follow-up control system is also widely used in the packaging process. For example, the automatic weighing system of the material can be regarded as a follow-up control system. The indicator value strictly and timely changes with the input (material weight).
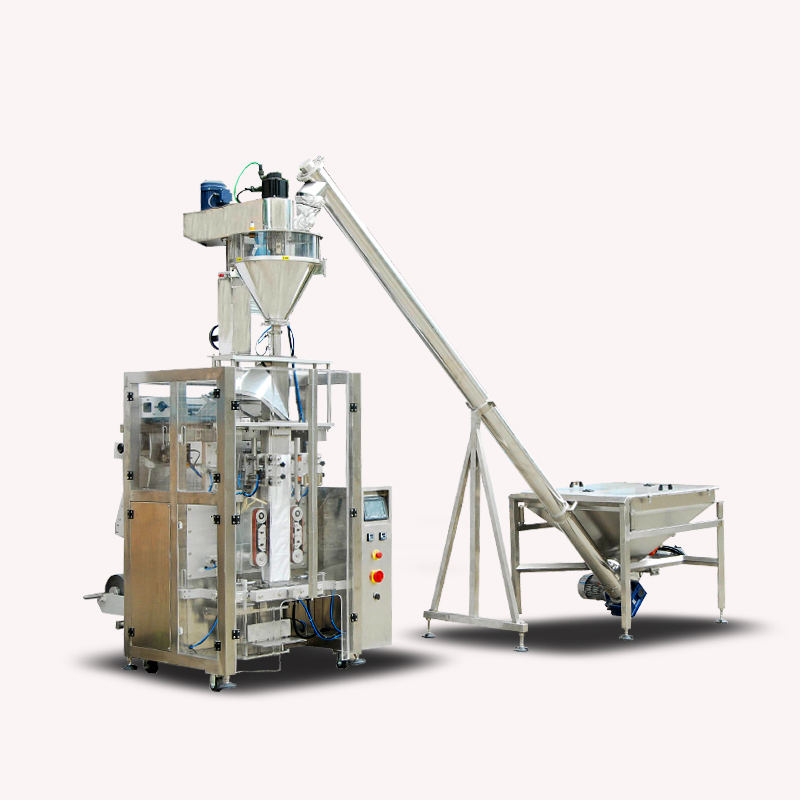
(二) Classification by feedback link
1. Open-loop control system
If there is no feedback loop between the output end and the input end of the system, the output has no effect on the control effect of the system. Such a system is called an open-loop control system. When the given voltage changes, the motor speed also changes, and the change in speed has no effect on the control. This kind of system can't withstand the influence of the load torque change on the speed. The open-loop system has a simple structure and no stability problem. However, it is affected by interference, and the control accuracy depends on the accuracy of each link and the size of the interference, which is usually low.
2. Closed-loop control system
There is a feedback loop between the output end and the input end of the system. The output has a direct impact on the control effect. Such a control system is called a closed-loop control system. The function of the closed loop is to use feedback to reduce the deviation. Generally, the closed loop system has high control accuracy.
However, the closed-loop system is more complicated than the open-loop system, and there is a stability problem, that is, the system output is far from a constant given value or cannot follow the change of the input amount, which makes the system in an unstable state. Therefore, when designing a closed-loop system, it is necessary to choose according to specific requirements.
(三) Classification according to the response characteristics of the system
1. Continuous control system
The parameter changes in the system are continuous, that is, the signal transmission of the system and the response of the controlled object are uninterrupted continuous or analog quantities. The aforementioned temperature control and motor speed control systems are all continuous control systems.
According to the relationship between the output and input of the system, this type of system can be divided into:
(1) Linear control system
The system consists of linear elements, and each link can be described by a linear differential equation, which satisfies the principle of superposition. That is, when several disturbances or control actions are acting on the system at the same time, the total effect is equal to the sum of the effects caused by each single action.
(2) Non-linear control system
Some links in the system have non-linear properties, such as saturation, dead zone, and friction. Such systems often need to be described by nonlinear differential equations, which do not satisfy the principle of superposition.
2. Intermittent control system
The intermittent control system is also called a discrete control system. The internal signal of the system is an intermittent quantity, which can be divided into:
(1) Sampling control system
Its characteristic is that the controlled continuous analog quantity is sampled by the sampling device at a fixed frequency, converted into a digital quantity and sent to a computer or numerical control device. After data processing or calculation, the control instruction is output, and the digital quantity is converted into an analog quantity. Control the controlled object.
(2) Switch control system
Intermittent working control system composed of switching elements. Since the switching element has only two distinct states of “on” and “off”, it cannot continuously reflect the change of the control signal, so the control that the system can realize must be intermittent. Common relay contactor control systems and programmable controller systems are switch control systems.
(四) Classification by production process parameters
According to the controlled process parameters, it can be divided into temperature control system, position control system, flow control system, speed control system and so on.
Tag: full automatic packing machine ; automatic packing machine ; powder packing machine ; single bucket elevator ; inclined bowl conveyor
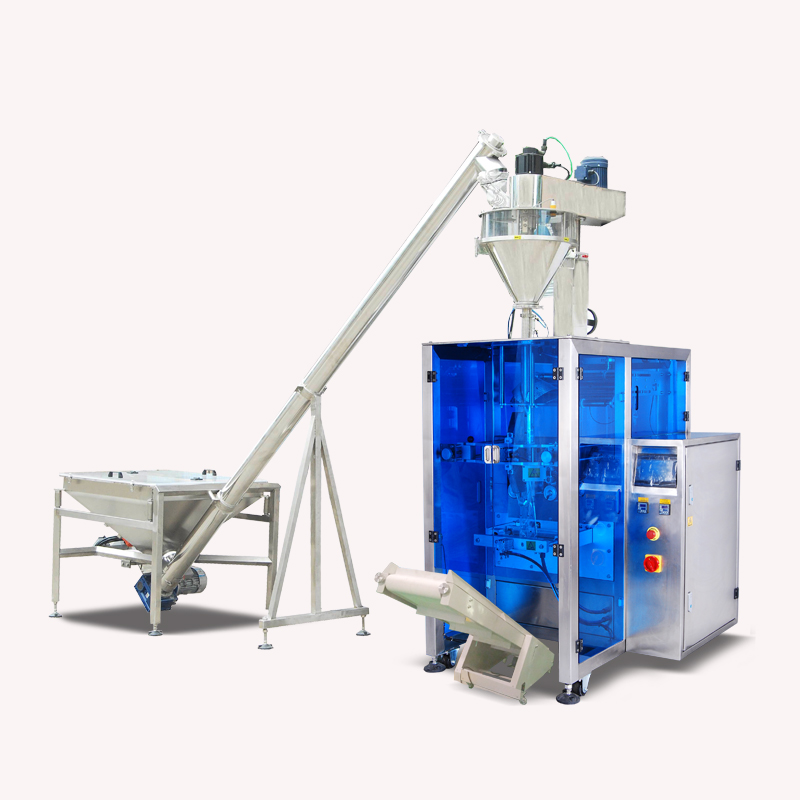
(—) Classification according to the change law of the input amount
1. Constant value control system
The so-called constant value is the abbreviation of constant given value. The given value of the system is unchanged, and the output of the system is required to be kept constant accordingly. During the packing process, some parameters are required to be kept at a normal standard value, which is the given value. Such as temperature control, material weight control, flow control, etc. are such systems.
2. Program control system
The given value of the system is a pre-determined time function that changes according to a predetermined law. The task of the system is to make the controlled quantity change according to a predetermined law with a predetermined accuracy.
3. Servo control system
Following control system is also called tracking control system. The characteristic of this type of system is that the given value is constantly changing, and the change law is unknown. The purpose of the control system is to make the controlled parameter follow the given value change quickly and accurately. The follow-up control system is also widely used in the packaging process. For example, the automatic weighing system of the material can be regarded as a follow-up control system. The indicator value strictly and timely changes with the input (material weight).
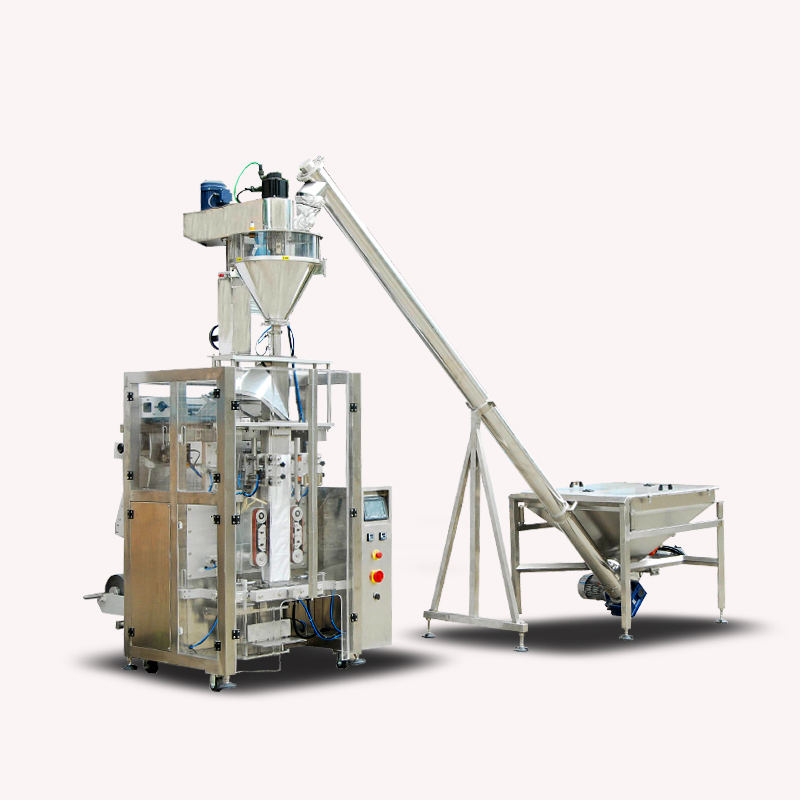
(二) Classification by feedback link
1. Open-loop control system
If there is no feedback loop between the output end and the input end of the system, the output has no effect on the control effect of the system. Such a system is called an open-loop control system. When the given voltage changes, the motor speed also changes, and the change in speed has no effect on the control. This kind of system can't withstand the influence of the load torque change on the speed. The open-loop system has a simple structure and no stability problem. However, it is affected by interference, and the control accuracy depends on the accuracy of each link and the size of the interference, which is usually low.
2. Closed-loop control system
There is a feedback loop between the output end and the input end of the system. The output has a direct impact on the control effect. Such a control system is called a closed-loop control system. The function of the closed loop is to use feedback to reduce the deviation. Generally, the closed loop system has high control accuracy.
However, the closed-loop system is more complicated than the open-loop system, and there is a stability problem, that is, the system output is far from a constant given value or cannot follow the change of the input amount, which makes the system in an unstable state. Therefore, when designing a closed-loop system, it is necessary to choose according to specific requirements.
(三) Classification according to the response characteristics of the system
1. Continuous control system
The parameter changes in the system are continuous, that is, the signal transmission of the system and the response of the controlled object are uninterrupted continuous or analog quantities. The aforementioned temperature control and motor speed control systems are all continuous control systems.
According to the relationship between the output and input of the system, this type of system can be divided into:
(1) Linear control system
The system consists of linear elements, and each link can be described by a linear differential equation, which satisfies the principle of superposition. That is, when several disturbances or control actions are acting on the system at the same time, the total effect is equal to the sum of the effects caused by each single action.
(2) Non-linear control system
Some links in the system have non-linear properties, such as saturation, dead zone, and friction. Such systems often need to be described by nonlinear differential equations, which do not satisfy the principle of superposition.
2. Intermittent control system
The intermittent control system is also called a discrete control system. The internal signal of the system is an intermittent quantity, which can be divided into:
(1) Sampling control system
Its characteristic is that the controlled continuous analog quantity is sampled by the sampling device at a fixed frequency, converted into a digital quantity and sent to a computer or numerical control device. After data processing or calculation, the control instruction is output, and the digital quantity is converted into an analog quantity. Control the controlled object.
(2) Switch control system
Intermittent working control system composed of switching elements. Since the switching element has only two distinct states of “on” and “off”, it cannot continuously reflect the change of the control signal, so the control that the system can realize must be intermittent. Common relay contactor control systems and programmable controller systems are switch control systems.
(四) Classification by production process parameters
According to the controlled process parameters, it can be divided into temperature control system, position control system, flow control system, speed control system and so on.
Tag: full automatic packing machine ; automatic packing machine ; powder packing machine ; single bucket elevator ; inclined bowl conveyor